What are the technical bottlenecks of Micro LED? How should domestic and foreign manufacturers layout
Today, it is reported that in the 10-year mobile phone launched this fall, Apple will use organic screen (OLED) for the first time in the company's history, supplied by Samsung Display. However, according to foreign media reports, Apple also acquired a company with micro-LED display technology, and is engaged in the research and development of display panels, which has caused certain concerns for Samsung, LG and other screen manufacturers.
According to the US technology news website Apple Insider, Apple will start producing micro-LED displays later this year, which will be used in the third generation of Apple watches. Currently, organic screens are used in Apple watches.
In the field of display panels, Apple has no technical reserves in the past. However, in 2014, Apple acquired a company called LuxVue, which acquired the company's micro-LED technology. In the past few years, this display panel technology has begun to attract industry attention, and Apple is also actively engaged. Development.
Micro-LED is optimistic as a new generation of display technology
In addition to liquid crystals, organic screens are considered as an alternative to liquid crystal panels. Before Apple, many mobile phone manufacturers such as Samsung Electronics have begun to use organic screens, which have better screen quality, more power saving, thinner thickness and curved design.
In fact, organic screen technology has been around for many years, but its cost is difficult to decline, but in the past few years, organic screen mass production technology has achieved breakthroughs, which has lowered costs. A large number of organic screen mobile phones and TV sets have appeared in the market, and there will be more related manufacturers in the future.
Micro LED Display is a new generation of display technology. The structure is miniaturized LED array, which is to thin, miniaturize and array the LED structure design, so that its volume is about the current mainstream LED size. At 1%, each pixel can be addressed and individually driven to illuminate, reducing the distance of the pixel from the original millimeter to the micrometer.
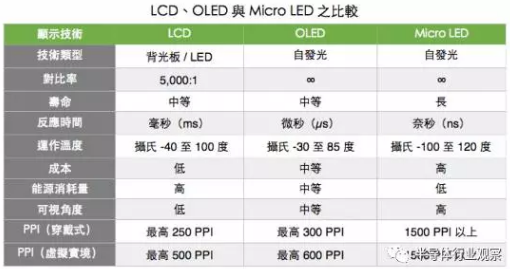
Inheriting the characteristics of LEDs, Micro LEDs include low power consumption, high brightness, ultra high resolution and color saturation, fast response speed, ultra power saving, long life, high efficiency, etc. The power consumption is about LCD. 10%, 50% of OLED. Compared with the OLED, which is also self-luminous display, the brightness is 30 times higher than the OLED, and the resolution is up to 1500 PPI (pixel density), which is equivalent to 5 times that of the Apple Watch using OLED panels up to 300 PPI. Better material stability and imageless imprinting are also one of the advantages.
The large size is the cost competition, and the competitive advantage of Micro-LED is not obvious. Micro-LEDs have great challenges in terms of large size. For many years, compared with LCD and OLED, LEDs have no advantage in cost, and from the actual investment and progress of Micro-LED, Micro-LED has no influence. Imagine that big. LCD has low cost, stable yield and strong competitiveness. Just like the LCD and PDP, the future competition between LCD and Micro-LED is not solely related to the competition of technology, but also involves the industry chain and ecological competition.
Process type and technology development
The process shrinkage for semiconductors and chips has reached its limit, and there is still considerable room for growth in manufacturing miniaturization. For the Micro LED process, there are currently three main types: Chip bonding, Wafer bonding, and Thin film. Transfer.
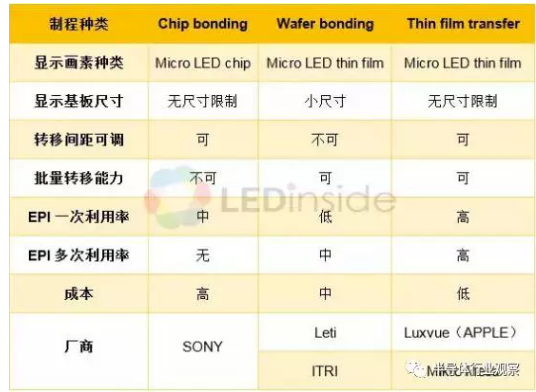
Chip bonding
The LEDs are directly cut into micron-sized Micro LED chips (including epitaxial films and substrates), and micron-sized Micro LED chips are bonded to the display substrate one by one by SMT technology or COB technology.
Wafer bonding
Inductively coupled plasma ion etching (ICP) on the epitaxial film layer of the LED directly forms a micron-scale Micro-LED epitaxial film structure. The fixed pitch of the structure is the spacing required to display the gradation, and then the LED crystal The circle (including the epitaxial layer and the substrate) is directly bonded to the driving circuit substrate, and finally the substrate is peeled off by physical or chemical mechanism, and only the micro-LED epitaxial film structure of 4 to 5 μm is formed on the driving circuit substrate to form a display.
Thin film transfer
The LED substrate is stripped by physical or chemical mechanism, the LED epitaxial film layer is carried by a temporary substrate, and then the micro-scale Micro-LED epitaxial film structure is formed by inductively coupled plasma ion etching; or, by inductively coupled plasma ion etching, A micron-scale Micro-LED epitaxial film structure is formed, and the LED substrate is stripped by physical or chemical mechanism to carry the LED epitaxial film structure with a temporary substrate.
Finally, according to the required display pixel pitch on the driving circuit substrate, the micro LED epitaxial film structure is transferred in batches by using a selective transfer jig, and is bonded to the driving circuit substrate to form a display.
Can Micro-LEDs challenge LCDs and OLEDs?
At present, Micro-LED can form two major application directions, one is the wearable market represented by Apple; Apple specializes in the small size application of Micro LED, and looks at the Lux LED display technology company LuxVue Technology, which acquired LuxVue in May 2014. , obtained a number of Micro LED patent technology, to speed up the layout of related technology patents. At the time, Apple's acquisition triggered market attention. Apple is expected to adopt a new generation of Micro LED technology on Apple Watch and iPhone. However, because it is not willing to rely too much on the panel factory, LuxVue will be taken over to obtain Micro LED. The technical dominance of the field.
One is the oversized TV market represented by Sony. The 55-inch "CrystalLEDDisplay" released by Sony in 2012 is the type of Micro LED Display technology. Its FullHD resolution uses a total of about 6.22 million (1920x1080x3) micro LEDs as a high-resolution display. The contrast ratio can reach one million to one. Saturation up to 140% NTSC, no reaction time and service life issues. However, due to the single-micro-LED embedding method, there are still many cost and technical bottlenecks in commercialization, so that there is no energy production so far.
This year, Sony's Micro-LED display at CES, CLEDIS, has excellent performance in terms of resolution, brightness and contrast. It has been Micro-LED.
At present, the Micro-LED market is concentrated on ultra-small size displays. For example, smart phones, smart watches, VR, etc. On these devices, Micro-LEDs compete primarily with OLEDs. The latter has already invested hundreds of billions of dollars on the road, and production capacity has been formed in large numbers. Micro-LED is still on the threshold of the most basic technology.
More importantly, smartphones, as the main market for small-size applications, still mean “large size†for Micro-LEDs, ie, high cost; VR, as the best potential stock, requires extremely high pixel density. OLED is already developing 1000PPI+ VR panels, which undoubtedly increases the difficulty of manufacturing Micro-LEDs; the cores displayed on smart watches need to be energy-saving, and there is no special requirement, but the total capacity of this market will be limited - because of its The display area of ​​a single unit is small.
Therefore, the choice of Micro-LED as the counter-attack direction, the first is to give up the medium and large size display market; the second is the core technology "still on the road", I am afraid the time is not waiting for people; the third is expected to have OLED before the target market QLED, "pressure mountain big".
Micro-LED development bottleneck
If Micro-LED is made into a display panel like LED display, it is technically feasible to use an area of ​​tens of inches to hundreds of inches, but it is far from commercial mass production, which requires higher speed. The huge amount of transfer technology, moving a small LED to the substrate, otherwise with the existing technology and yield, to build a usable display, taking too long, can not mass production.
According to LED inside statistics, the manufacturing cost of Micro-LED display technology is still 3-4 times higher than that of existing display products. Therefore, manufacturers are actively increasing the added value of products and improving chip and transfer technology yield. The cost reduction target is estimated to take 3 to 5 years to replace the existing LCD products.
Micro-LED products require high wavelength uniformity, and the uniformity of wavelengths of LED products for small pitch is more demanding. At present, the wavelength uniformity of blue LEDs under mass production standards is required to be ±5~12nm. However, the uniformity of wavelengths of small-pitch display screens is even as low as ±1-1.5 nm. If it is a Micro LED, the requirements will be more stringent.
In other words, under the mass production scale, the high-precision transfer process to improve the process yield must be at least 99.9% higher than the 99.999%.
In this way, the PCB boards that the industry needs to use must also be able to fulfill the requirements of customization. Through the development of thin line width/line spacing and small boreholes, it is possible to carry huge quantities through such ultra-high-density lines. Micro-LED pixels provide high-resolution, high-quality display for consumers and users.
In addition, Micro-LED manufacturing costs remain high, because the related technology bottlenecks still need to be broken, such as the improvement of yield, Mass Transfer technology, and the industry involved across LEDs, semiconductors, and panels. Upstream and downstream supply chains, such as chips, machines, materials, testing equipment, etc., are different from the previous specifications, which raises the threshold of technology, and the integration of communication between different industries also increases the development time.
The key transfer technology in the micro-LED manufacturing process can be used to transfer tiny LEDs, as well as transfer small electronic components such as sensors, making the application of Micro-LEDs more imaginative. In the future, in the fields of car display, VR device, even AR projection, optical sensing, fingerprint identification, etc., there is an opportunity for Micro-LED technology to shine.
In addition, for the development of Micro-LED, if you want to achieve the manufacture of large-scale micro-LED display, you must combine the three major different expertise and supply chain including LED manufacturing, display manufacturing and technology transfer and assembly. .
Compared to traditional displays, the supply chain of Micro-LED displays is complex and lengthy, and each process is critical, and managing each aspect effectively can be challenging. No one can solve all the problems, and it seems unlikely that full vertical integration will be achieved.
Mainly involved in the development of Micro-LED companies
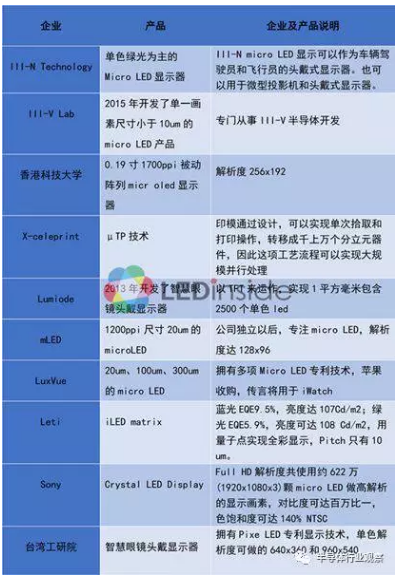
Micro-LED's international companies include Sony, LG, Nichia, Sharp, etc., and the company mLED from the University of Strathclyde, Texas Tech University (Texas Tech University) ), the French Atomic Energy Agency's Electronic and Information Technology Laboratory (Leti), and X-celeprint, which was spun off from the University of Illinois, are also actively developing Micro-LED technology.
Many large Taiwanese companies have also invested in technology research and development, including semiconductor startups such as PlayNitride, Industrial Research Institute, AUO, Innolux and Jingdian.
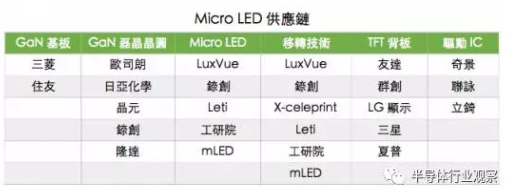
Sony
At the InfoComm show in June 2016 and the IFA show in Germany, Sony demonstrated the "CLEDIS" LED display technology that uses Micro LED components as a pixel. This new technology, which is described as capable of challenging OLEDs, is very mysterious.
Sony CLEDIS technology is actually a small-pitch LED display technology with a dot pitch of 1.2mm. This small-pitch LED display is a single pixel through the combination of RGB three-color LED devices, encapsulating multiple pixels into screen elements, and then dropping multiple elements to form a complete display unit, and finally we see the large-size LEDs. The screen is mostly formed by seamlessly splicing the display unit.
This type of display unit is combined to change the size and aspect ratio of the screen depending on the application and location. The screen borders of each component are very thin, placed up and down and left and right together to create a large screen with almost no seams. Imagine mainly for B2B applications, including digital signage, public large screens, exhibition hall displays, and automotive design reviews.
Sharp, Nichia Chemical
As the application of new technology of Micro-LED has the opportunity to set off the destructive innovation of the display industry, attracting international manufacturers to try, and launching a new wave of industry competition for breaking through the technology checkpoints, the industry has announced that Apple intends to introduce Micro-LED, prompting the Hon Hai Group to decide Invested in the research and development of Micro-LED, and has been approved by the chairman Guo Taiming, and will be the Asian strategic strategy partner of the Group Group Panel Factory in Japan, to seize the strategic position of the next generation of displays.
Hon Hai pointed out that the Group has plans to use resources for relevant investment in the application and development of new technologies. It is hoped that by technology mastery, it will lay the foundation for market advantage.
According to Nichia, the company has been working on Micro-LED for more than 10 years and has leading technology, which will accelerate the commercialization of Micro-LED in the future. The first stage is to introduce a surface light source module, which can not only achieve local dimming, but also can realize a flexible display panel on a flexible substrate. After two years, it can be extended to the second stage. The ultimate goal is to realize Micro-LED.
Jingdian, Ronda, Innolux
Jingshi spokesperson Zhang Shixian publicly stated that due to the small size of the Micro-LED, the epitaxial and grain processing of the crystal electric power should be jointly developed with the transfer equipment and system applications. In the process of epitaxy and grain, the success rate of Micro-LED is high. As for whether it can be mass-produced and shipped in 2017, it will be very hard.
Su Fengzheng, chairman of Ronda, also said that Micro-LED is a new technology and new application, and has the opportunity to increase the amount of LED used. This is also one of the directions for the application of Ronda's new layout. At present, many companies are in the process of layout, and the progress is different. As for when it is possible to commercialize mass production, it believes that the learning curve of poor initial yield and more people's investment after improvement can not be omitted.
Wang Zhichao, chairman and chief executive of Qunhuang, pointed out that the soft display will be a trend, and there are still other technical options such as Micro-LED.
Accumulation, Industrial Research Institute
The front desk of the company is an LED driver IC manufacturer accumulating announcement. The board of directors of the company has decided to cooperate with the Taiwan Industrial Technology Research Institute (ITRI, referred to as “Taiwan Institute of Technologyâ€) to develop the “ultra-small-pitch LED digital display moduleâ€. Micro-LED display module.
Accumulation pointed out that it is mainly in response to market development and enhance competitiveness, so it cooperated with the Taiwan Institute of Technology to develop.
In addition, the ISE 2017 exhibition, which was previously held in Amsterdam, the Netherlands, has new products in the mainstream mainstream LED display screen market. In response to the diversified demand for small-pitch LED displays, from the solution of common display problems at small pitches to leasing, 24-hour continuous power applications (central control rooms, shopping malls), Accumulation Technology is focusing on “simple, intelligent and superiorâ€. The latest Hawkeye series solutions.
How to arrange Micro-LED for domestic manufacturers
At present, domestic LED manufacturers have begun to develop Micro-LED technology. It is understood that last year, Liard launched the AMD P0.9mm HD seamless wall, which is the first LED display on the market to achieve mass production of less than 1 mm pitch, but mainly used in indoor monitoring. The field, unlike Apple and Sony, focuses on wearable and large-screen TV.
Although domestic LEDs have formed a certain scale in the commercial market, domestic LED equipment has accelerated the process of localization of LEDs. However, most domestic LED manufacturers have small revenues. Currently, they pay more attention to the LED commercial market itself. For micro-LEDs like this. There are relatively few forward-looking technical inputs, and there are not many discussions on Micro-LED in domestic LED-related conferences.
Micro-LED is cut from the chip angle. Domestic small-pitch LEDs are from the perspective of the display screen. Although they are all made of small-pitch LEDs, the scales of the two are different. There is no enterprise in the domestic LED industry that can vertically integrate the entire industry chain. Each enterprise has its own focus on one chip, and the chip is used as a chip. The package is only packaged and used for application. Moreover, most of the small-pitch LEDs are now concentrated in the application layer, and have not yet extended from the application layer to the upstream industry chain, and have not reached the chip layer. At present, the small-pitch LED of domestic energy production is P1.2~1.5 mm, and the smallest is P0.9 mm.
Apple and Sony Micro-LED are both made of LED display driver circuit with normal CMOS integrated circuit manufacturing process, and then use MOCVD machine to make LED array on integrated circuit, thus achieving a smaller micro-display size. Up to 100 microns, domestic small-pitch LEDs are an order of magnitude worse than Apple and Sony's Micro-LEDs.
At present, the upstream organic luminescent materials are mainly in the hands of foreign manufacturers such as Japan, South Korea, the United States, and Germany. There is no substitute product in China. Domestic enterprises mainly provide intermediates and monomer crude materials for organic materials for international material manufacturers. With the increase in demand for panels, the sales volume of domestic intermediates and monomer crude products is expected to increase substantially.
Secondly, the current development of Micro-LED is still in a preliminary stage, and domestic enterprises have been in the layout, not to say that they are at the same level, but the difference is not as large as the panel LED was originally developed in China.
Finally, if Micro-LED wants to open the distance, it will be more patent competition in the future. This is also the point that domestic companies need to consider when laying out Micro-LEDs.

LC Band Pass and Low Pass Filter
Lc Band Pass Filter,Low Band Pass Filter,Rf Band Pass Filter,Adjustable Bandpass Filter
Chengdu Zysen Technology Co., Ltd. , https://www.zysenmw.com